火箭一级发动机舱段壳体屈曲失稳试验
压扁“汽水罐”也是火箭科学 Crushing “Cans” Is Rocket Science
这就是NASA工程师面临的挑战。
圆柱形火箭外壳的负载类似于汽水罐。 它们在提升载荷下的强度被称为“壳体屈曲失稳因子”或SBKF。 原始的SBKF模型是在20世纪60年代开发的。 当时可用的技术选择限制了这些模型的准确性。 其结果是,火箭的设计必须是过度设计的安全性,并且增加了大量不必要的重量。
今天,诸如有限元建模等技术允许分析更详细的模型。 但是,这些模型必须通过对真实样本的测试来验证。 实际样品在载荷下的位移是验证过程的关键部分,当涉及到这些数据时,实验数据绝对更好。
美国宇航局NASA启动了一个SBKF模型的升级计划。 2011年3月23日,NASA成功进行了一个全尺寸试样失效测试,这是一个重要的里程碑。 该测试在互联网上直播,并存档在www.ustream.tv(NASA电视频道:World’s Largest Can Crusher)。
为了获得他们所需的位移数据的数量和质量,NASA依赖于Correlated Solutions, Inc提供的3D数字图像相关(DIC)系统实现。将随机黑白散斑图案应用于样本表面(见照片右侧并注意参照标本下面的移动升降机的尺寸)。 图像采集器连续监测样品的整个表面,VIC-3D软件允许NASA工程师实时监测详细的全场三维位移和应变数据! 共有7个VIC-3D系统用于覆盖整个360度的区域。
实验中样品被加压至1psi并逐渐加载至超过800,000磅。 虽然外壁光滑,但内部肋和焊缝所受的影响可以在离面位移数据w或Δz中清楚地看到(见左图)。 正如视频中的一位NASA测试工程师所说:“这是我们在测试过程中观察到的实时数据类型,因此我们确切的知道正在发生什么。”
实时的VIC-3D数据被用于监测和控制测试过程。 高速摄像机在破坏发生时以每秒3,000帧的速度捕获图像。 并且所有同步记录的视频图像都被保存了。 因此,美国国家航空航天局NASA的工程师可以在整个测试周期内获得样本的详细的全场3D变形测量。
DIC数字图像相关技术在美国宇航局SBKF测试计划中发挥了关键性作用。 正如视频所显示的那样,VIC-3D系统提供的信息是任何其他技术都难以想象的。 与有限元分析建模结合使用,它将使NASA为未来的火箭减轻重量并增加有效载荷。
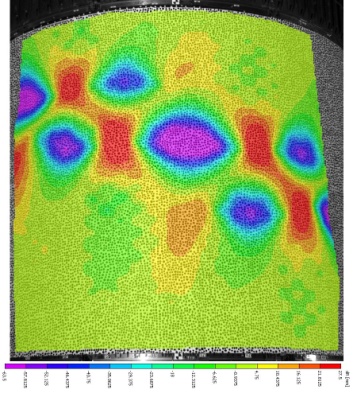
For most of us, the crushing of aluminum cans is a familiar scene. But, what if you had to precisely model the crush load of a can? And, what if the “can” was a complex structure with a diameter of 27.5 feet? This was the challenge facing NASA engineers.
Cylindrical rocket shells are subject to loads similar to soda cans. Their strength under lifting loads is referred to as a “Shell Buckling Knockdown Factor” or SBKF. The original SBKF models were developed back in the 1960’s. The available technology of the era limited the accuracy of these models. As a result, rocket designs had to be over-engineered for safety, and were unnecessarily heavy.
Today, technologies such as Finite Element Modeling permit more detailed models. But, these models must be validated through the testing of real specimens. Actual specimen displacements under load are a critical part of the validation process, and when it comes to this data, more is definitely better.
NASA started a program to update their SBKF models. An important milestone was reached on March 23, 2011, when NASA successfully tested a full-scale specimen to failure. This test was broadcast live on the internet, and is archived at www.ustream.tv (NASAtelevision: World’s Largest Can Crusher).
To get the quantity and quality of displacement data they would need, NASA relied on 3D Digital Image Correlation (DIC) systems supplied by Correlated Solutions, Inc. Random black-and-white patterns were applied to the surface of the specimen (see photo right and note the size of the mobile lift below the specimen). Digital cameras continuously monitored the entire surface of the specimen, and VIC-3D software allowed NASA engineers to monitor detailed full-field three-dimensional displacement and strain data in real-time! A total of seven systems were used to cover the entire 360 degree area.
The specimen was pressurized to 1psi and gradually loaded to more than 800,000 pounds. Although the outer wall was smooth, the effects of internal ribs and welds can be plainly seen in the out-of-plane displacement data w or Δz (see image left). As one NASA test engineer in the video feed put it: “this is the type of real time data we get to observe during the test so we know exactly what’s going on.”
The real-time VIC-3D data was used to monitor and control the testing process. High-Speed cameras captured images at 3,000 frames per second at the moment of failure. And, all of the synchronized video images were saved. As a result, NASA engineers have access to detailed, full-field, 3D deformation measurements of the specimen, throughout the entire test cycle.
Digital Image Correlation has played a key role in the successful NASA SBKF test program. As the video footage shows, the VIC-3D system provides information that would be unimaginable with any other technology. Used in conjunction with FEA modeling, it will allow NASA to decrease weight and increase the payload of future rockets.
照片由NASA公众推广网站提供 Photos courtesy of NASA public outreach site: www.nasa.gov/topics/technology/features/buckling2.html
应用案例视频 Application Example Video
NASA对 Digital Image Correlation技术的介绍在视频的3:55开始
关于该项目的更多信息可访问 More Information on this project:
VIC-3D实时全场数据测量特性 Real-Time Features
|
|
|
|
火箭推进系统流衬套的振动测量
NASA曾评估航天飞机推进系统中使用的流衬套,以确定振动是否会导致开裂。 由于衬套工作时可能受到一定范围的振动频率的影响,而哪种频率下会产生最大的振动应变是未知的。
A flow liner used in the propulsion system on the space shuttle was under evaluation to determine whether vibrations could result in cracking. The liner could be subject to a range of vibration frequencies, and it was not known which would produce the greatest vibratory strains.
技术挑战 Challenges
被测试件很复杂,这意味着该部件的整体响应将无法预测。 由于它结构自重很低,这意味着与试件的任何接触都可能会改变其力学响应。 虽然主要关注的领域不是很大,但它的结构具有几何特征,这使得难以预测峰值应变的位置。 也很难知道峰值应变的区域是否足够大,是否可用应变片进行识别。 加之需要模拟飞行条件所需的高频率,使测试更加复杂。 测试最终需在高达6kHz的频率下测量振动响应。
The specimen under test was complex, which meant that the overall response of the part would be impossible to predict. It was also fairly lightweight, which meant that any contact with the specimen could be expected to alter its response. Although the areas of primary concern were not very large, they included geometric features which made it difficult to predict the location of peak strains. It was also difficult to know whether the areas of peak strain would be large enough to be identified with strain gages. This test was further complicated by the high frequencies required to simulate flight conditions. Vibration response was measured at frequencies up to 6kHz.
解决办法 Solution
CSI公司提供了一套Vic-3D系统及振动同步模块,确保可以精确地从振动试件中采集数据,而且无需高速摄像机。 由于DIC测量不需要接触试件,因此试件的运动不受测量系统的影响。 在整个图像区域获得应变测量值,从而确定最大应变的真实位置。 由于Vic-3D具有很高的空间分辨率,即使峰值应变集中在很小的区域,研究人员也能够获得准确的测量结果。
Correlated Solutions provided a Vic-3D system and a vibration synchronization module designed to accurately capture data from vibrating specimens without the expense of high-speed cameras. Because the measurements do not require contact with the specimen, the specimen’s movement was not affected by the measurement system. Strain measurements were obtained over the entire image area, allowing the true location of the maximum strain to be identified. Because of Vic-3D’s high spatial resolution, researchers were able to obtain accurate measurements even when peak strains were concentrated in a very small area.
exx max= ±200µε eyy max= ±300µε
相关链接 Links
Read about the Vibration Fatigue Module for more information on this technology.